State-of-the-art technology in plastic extrusion for modern industries
Comprehending the Basics and Applications of Plastic Extrusion in Modern Production
In the realm of modern-day manufacturing, the method of plastic extrusion plays an important role - plastic extrusion. This detailed procedure, including the melting and shaping of plastic with specialized passes away, is leveraged throughout numerous markets for the development of varied products. From automobile parts to customer goods product packaging, the applications are huge, and the potential for sustainability is equally impressive. Unraveling the principles of this procedure reveals truth convenience and capacity of plastic extrusion.
The Basics of Plastic Extrusion Process
While it may show up facility, the fundamentals of the plastic extrusion procedure are based upon reasonably simple principles. It is a manufacturing procedure where plastic is melted and after that shaped right into a continuous account via a die. The raw plastic material, usually in the form of pellets, is fed into an extruder. Inside the extruder, the plastic undergoes heat and stress, causing it to thaw. The molten plastic is then required with a shaped opening, referred to as a die, to form a long, constant item. The extruded product is cooled and afterwards cut to the preferred size. The plastic extrusion process is thoroughly used in various markets because of its cost-effectiveness, convenience, and efficiency.
Various Sorts Of Plastic Extrusion Techniques
Building upon the basic understanding of the plastic extrusion procedure, it is required to explore the various techniques associated with this production method. Both main techniques are profile extrusion and sheet extrusion. In account extrusion, plastic is melted and formed into a constant account, often used to produce pipes, poles, rails, and window frames. In contrast, sheet extrusion develops big, level sheets of plastic, which are typically additional processed into products such as food packaging, shower curtains, and auto parts. Each method needs specialized equipment and specific control over temperature level and pressure to make certain the plastic maintains its shape throughout air conditioning. Comprehending these methods is key to making use of plastic extrusion effectively in modern-day manufacturing.

The Duty of Plastic Extrusion in the Automotive Industry
An overwhelming bulk of components in contemporary cars are items of the plastic extrusion procedure. This process has reinvented the automotive industry, transforming it right into a much more effective, cost-effective, and flexible manufacturing industry. Plastic extrusion is largely utilized in the production of numerous car elements such as bumpers, grills, door panels, and control panel trim. The process offers an attire, constant result, allowing producers to create high-volume get rid of wonderful accuracy and very little waste. The agility of the extruded plastic visit the website components adds view website to the general reduction in automobile weight, improving gas effectiveness. The sturdiness and resistance of these parts to heat, cool, and influence improve the durability of autos. Hence, plastic extrusion plays a critical duty in auto manufacturing.
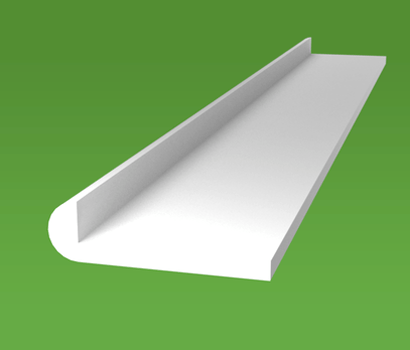
Applications of Plastic Extrusion in Durable Goods Manufacturing
Beyond its considerable influence on the automotive market, plastic extrusion confirms equally effective in the world of durable goods making. This procedure is essential in creating a large array of items, from food packaging to household devices, playthings, and also clinical tools. The adaptability of plastic extrusion allows suppliers to develop and create intricate forms and dimensions with high accuracy and efficiency. Due to the recyclability of numerous plastics, extruded elements can be recycled, minimizing waste and expense (plastic extrusion). The adaptability, flexibility, and cost-effectiveness of plastic extrusion make it a favored choice for numerous customer goods manufacturers, adding significantly to the market's growth and innovation. However, the ecological ramifications of this prevalent use need careful consideration, a topic to be discussed better in the subsequent area.
Ecological Influence and Sustainability in Plastic Extrusion
The pervasive usage of plastic extrusion in manufacturing invites analysis of its environmental implications. Efficient equipment decreases power use, while waste management systems reuse scrap plastic, reducing raw product demands. Despite these renovations, even more innovation is required to reduce the ecological impact of plastic extrusion.
Verdict
In conclusion, plastic extrusion plays an important duty in modern manufacturing, especially in the automobile and consumer products industries. Understanding the basics of this process is key to maximizing its applications and benefits.

The plastic extrusion process is extensively used in different industries due to its adaptability, effectiveness, and cost-effectiveness.
Building upon the fundamental understanding of the plastic extrusion procedure, it is essential to discover the different methods included in this production technique. plastic extrusion. In contrast, sheet extrusion develops big, flat sheets of plastic, which are generally further refined into items such as food packaging, shower drapes, and automobile parts.A frustrating majority of components in modern cars are items click now of the plastic extrusion process